| Injector system tested | Liquid placement assessment | Crop residue cover and soil disturbance | Odour | Draft measurements | Summary
Liquid manure injection offers a number of advantages over broadcasting:
- fewer odours
- ability to place nutrients directly into the seedbed
- reduce loss of fertilizer value
Because of these advantages, more manure applicators are using liquid manure injection equipment than ever before. This increase in usage prompted Alberta Agriculture, Food and Rural Development's Technical Services Division to test the performance of five common liquid manure injection openers:
- two low-disturbance injectors (K-Hart and Yetter)
- two high-disturbance injectors (Spike and Sweep)
- an aerator (Aerway)
These five systems were each tested for several features:
- liquid placement
- soil disturbance
- crop residue and disturbance
These tests were done while applying water at rates ranging from 34,000 to 146,000 L/ha (3,000 - 13,000 gal/ac) and moving at ground speeds ranging from 2.6 to 10.6 km/h (1.6 - 6.6 mi/h).
Each system was also evaluated for odour control at an application rate of 67,000 L/ha (6,000 gal/ac) of liquid hog manure at 0, 4, and 24 hours after injection. Draft tests were performed for each injector (with the exception of the Aerway) at depths ranging from 8 to 15 cm (3 - 6 in).
Injector Systems Tested
Yetter. The Yetter Avenger injector system (Figure 1) consisted of a 64 cm (25 in) diameter offset disk angled at 5 degrees to the direction of travel. A 38 cm (15 in) diameter rubber cleaning wheel was mounted to the exposed side of the disk and a metal scraper was mounted on the protected side of the disk. A drop tube was located directly behind the offset disk. The Yetter included a set of concave closing disks attached to the frame behind the drop hose. The closing disks were removed during testing as they produced a lot of soil disturbance.

Figure 1. Yetter Avenger injector
K-Hart. The modified K-Hart injector system was a K-Hart fertilizer bander modified to perform liquid manure injection (Figure 2). The original bander consisted of a 46 cm (18 in) diameter coulter and a drop-hose housing for fertilizer. Changes were made to the drop hose housing in order to fit in a liquid manure drop hose.
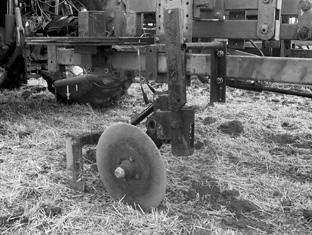
Figure 2. Modified K-Hart injector
Sweep. The Sweep injector system consisted of a 26.7 cm (10.5 in) wide sweep opener mounted on a 5 cm (2 in) wide C-shank (Figure 3). A metal tube was mounted directly behind the sweep to hold a drop hose.
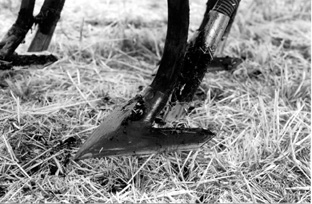
Figure 3. Sweep injector
Spike. The Spike injector system had a 5 cm (2 in) wide spike opener mounted on a 5 cm (2 in) wide C-shank (Figure 4). A metal tube was mounted directly behind the spike to hold a drop hose.
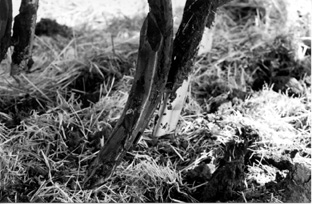
Figure 4. Spike injector
Aerway. The Aerway system consisted of a series of spikes mounted on an axle (Figure 5). A drop hose was mounted behind each spike set. The spikes were spaced 19 cm (7.5 in) apart and penetrated the soil creating a soil aeration effect. The drop hoses then delivered the liquid to the soil surface, and to the spike holes in the soil surface.
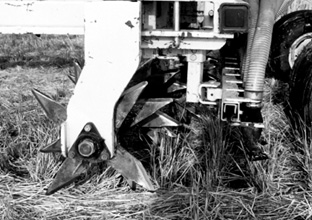
Figure 5. Aerway aerator
Liquid Placement Assessment
The liquid placement assessment was carried out over several days in heavy clay loam Dark Brown Chernozem soil. This soil was very dry and hard. Immediately after injecting the soil with the different amounts of water, testers watched for several factors:
- pooled liquid
- wet soil
- any other evidence of liquid on the surface
Ratings. Table 1 shows the average liquid placement rating results.
Table 1. Average liquid placement ratings |
Rate L/ha (gal/ac) | 34000 (3000) | 56000 (5000) | 79000 (7,000) | 101000 (9,000) | 124000 (11,000) | 146000 (13,000) |
Low disturbance (disk injectors) |
Yetter | 1.25ab | 1a | 1.5a | 1.5a | 1.25a | 1.75a |
K-Hart | 2c | 2b | 2a | 2.5bc | 2.75c | 3b |
High disturbance (shank injectors) |
Sweep | 1a | 1.5ab | 1.5a | 1.75ab | 2b | 2a |
Spike | 1.5b | 1.5ab | 1.5a | 1.75ab | 1.75ab | 1.75a |
Aerator |
Aerway | 3d | 3c | 3b | 3c | na | na |
Rating scale: 1 = no evidence of liquid on surface, 2 = evidence in furrow only, 3 = evidence on surface outside of furrow
Averages within a column followed by the same letter are not significantly different (P<0.05)
The goal of the injectors was to apply the liquid at or below the soil surface:
- The Aerway pooled the liquid manure on the surface at all rates.
- When using the other injectors, evidence of liquid manure increased as the manure rate increased.
- The K-Hart injector pooled the manure at the highest rate.
Crop Residue Cover and Soil Disturbance
Disk injectors produce considerably less residue and soil disturbance than do shank injectors.
The disk injectors and the Aerway had less than 30 per cent soil disturbance at all ground speeds, making them compatible with low-disturbance cropping systems such as direct seeding and forage production.
The shank injectors are incompatible with low-disturbance cropping systems. However, disk injectors may not penetrate hard dry soil as well as shank injectors.
Odour
With the exception of the Spike, all the equipment tested provided acceptable odour control immediately after application and in the hours following injection:
- The Spike showed increased odour emissions 24 hours after injection, but this result may have been caused by high background odours or an error in measurement.
- Odour emissions lessened rapidly during the hours following injection for all treatments as the manure was being absorbed into the soil and along fracture lines.
- The odour concentrations at 4 and 24 hours were below detectable levels for the odour measuring panel for all treatments.
Draft Measurements
Draft forces were measured using a cart with one injector for all systems except the Aerway at various depths. Only the Yetter was able to penetrate to a 15 cm (6 in) depth because of its high-force trip spring and design. The Spike and Sweep were operated with a medium-duty shank and trip; they might have reached deeper depths with a heavy-duty shank and trip.
The draft measurements were taken under higher than normal soil moisture conditions in well-packed soil. Testing showed the following:
- The K-Hart and Yetter produced the lowest draft measurement at the shallow depth.
- The Spike and Sweep produced the highest draft measurement.
- The draft of the Yetter increased substantially as the depth increased. Its draft at 6 in (15 cm) is similar to the draft of the Sweep at 5 in (13 cm).
The draft requirement results are shown in Table 2.
Table 2. Draft resultsz |
Depth | 8 cm (3 in) | 10 cm (4 in) | 13 cm (5 in) | 15 cm (6 in) |
Injector | N
(lbf) | kW
(hp) | N
(lbf) | kW
(hp) | N
(lbf) | kW
(hp) | N
(lbf) | kW
(hp) |
K-Hart | 310
(70) | 0.56
(0.75) | 490
(109) | 0.89
(1.2) | 1590
(358) | 2.8
(3.8) | nay | nay |
Spike | 1580
(355) | 2.8
(3.8) | 1950
( 438) | 3.5
(4.7) | nay | nay | nay | nay |
Sweep | 2060
(462) | 3.6
(4.9) | 2410
(542) | 4.3
(5.8) | 2550
(573) | 4.5
(6.1) | nay | nay |
Yetter | 600
(134) | 1.0
(1.4) | 890
(199) | 1.6
(2.1) | 1450
(326) | 2.6
(3.5) | 2360
(531) | 4.2
(5.7) |
y Injector did not penetrate soil to required depth
z Draft measurements performed at a ground speed of 6.7 km/h (4.0 mi/h) with one injector
Summary
When selecting manure injection technology, it is important to weigh the pros and cons of each system being considered. Several conclusions were shown in the study:
- High-disturbance injection technology controls odour, but results in a lot of residue and soil disturbance.
- Low-disturbance injection technology provides minimal residue and soil disturbance, but does not control odour as well as high-disturbance injection equipment (although all produced acceptable results).
- All technologies provide acceptable nutrient placement.
A producer's individual situation should dictate which system to use. For example, a producer practicing direct seeding may choose low-disturbance injection while a producer practicing tillage may choose high-disturbance injection.
For more information
For more information on this study, see the full report called Performance Evaluation of Five Liquid Manure Injection Systems (676 Kb). Call the Alberta Ag-Info Centre at 1-866-882-7677 for further information.
Prepared by:
Karen Stewart - Livestock Environmental Specialist
Technical Services Division
Source: Agdex 743-1. August 2005. |
|