| Why anhydrous ammonia? | How does NH3 work? | NH3 system and planter combination | NH3 safety issues
Many farmers are interested in adding an anhydrous ammonia application system to their one-pass direct seeding planter systems. This is a practical option if a suitable ground opener can be found that ensures separation of the anhydrous ammonia (NH3) from the seed row and also seals the soil surface to prevent escape of NH3. However, NH3 requires careful handling to ensure personal safety.
Why Anhydrous Ammonia?
Several characteristics make NH3 a practical choice for many direct seeding farmers:
Effectiveness as nitrogen fertilizer source: Most research shows that nitrogen supplied as NH3 is used by crops as effectively as nitrogen from any other source.
Cost: At some locations and in some years, NH3 may offer a price advantage over other forms of nitrogen. The cost of handling and trucking NH3 is included in the price per tonne.
Field capacity: The field capacity (acres per hour) of a direct planting system depends on how often the planter must stop to refill with seed and fertilizer. The combination of an air seeder, for seed and granular fertilizer other than nitrogen, and an NH3 tank, for nitrogen, allows the greatest number of acres between fills. NH3 is 82 per cent nitrogen, and this high concentration (expressed as 82-0-0) allows 1.78 times more acres to be planted per tonne of fertilizer as compared to urea which is only 46 per cent nitrogen (46-0-0). A sample calculation is shown below.
Storage and trucking: NH3 is delivered to the field by the fertilizer dealer, saving both storage and trucking for the farmer.
Sample calculation of field capacity comparison of nitrogen in dry granular form versus
NH3
A dual-tank air cart with a 90-bushel tank applying seed and a 140-bushel tank applying 34-17-0 fertilizer at 60 pounds/acre of nitrogen is limited to 40 acres between fills. The 90-bushel tank of barley seeding at 85 pound/acre would cover 53 acres. However, by adding a 1750-gallon NH3 tank, the nitrogen source covers 120 acres between fills, and the field capacity limit is now the barley seed from the 140-bushel tank covering 100 acres. (Phosphate fertilizer (P205) is being applied through the 90-bushel tank, but is not the limiting factor.) |
How Does NH3 Work?
At normal temperatures and pressures, NH3 is a gas. For agricultural use, NH3 is stored in its liquid form in a pressure tank at about 100 pounds per square inch gauge pressure (psig) at 20°C. As the temperature rises, the pressure needed to keep it liquid also rises. When it is not under pressure, the boiling point of NH3 is -34°C, very similar to that of propane. At or below -34°C, NH3 is a liquid even without pressure.
The pressure in the tank causes the liquid NH3 to flow through the open valve to the metering system. It goes through the meter and distribution system to the outlet in the ground opener and into the soil.
As the NH3 is released from the tank into the distribution system, the sudden drop in pressure from about 100 psig to about 0 psig causes rapid boiling of the NH3 (that is, changing from a liquid to a vapour) because its temperature is much higher than -34°C. The rapid boiling converts the NH3 into a mixture of gas bubbles and liquid drops flowing rapidly through the system.
Vaporization of NH3 requires energy. Therefore vaporizing NH3 takes heat from the surrounding air, the equipment handling the liquid or the liquid NH3 itself. The cold lines and valves become covered with frost from water vapour in the air. The rapid absorption of heat can be a safety problem.
NH3 vapour is lighter than air so it rises. The vapour is colourless. The white "puffing" which results when NH3 escapes is water vapour condensed from the air by the cooling effect of the liquid NH3 as it boils.
In some systems, NH3 goes through a cold flow converter between the meter and the distribution system. In the cold flow converter, there is a swirling mass of vaporizing NH3. The vaporizing NH3 draws heat from the surrounding liquid NH3. By the time about 15 per cent of the NH3 vaporizes, the rest of the NH3 is cooled to its liquid temperature (-34°C) at 0 psig. After the liquid NH3 has been injected into the soil, it gradually vaporizes.
Once in the soil, the NH3 finds another hydrogen ion (H+) on a water molecule or in the soil organic matter and becomes NH4 (ammonium). The crop can take up NH4 directly through its roots. Some NH4 is consumed by micro-organisms and released as NO3 (nitrate), which is also used directly by the crop.
NH3 System and Planter Combination
A direct seeder with NH3 is simply a combination of two machines on one chassis. An air seeder handles the seed and certain fertilizer types, and the added NH3 system handles that. However, some extra parts or features should be added or considered when an NH3 system is added to a planter.
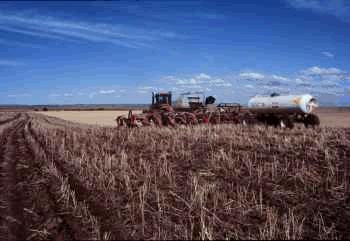
Anhydrous ammonia application in a one-pass seeding system.
Safety couplers
If the NH3 tank is pulled behind the air tank of an air seeder, the main delivery hose must have safety break-away couplers at both the rear of the air tank and the rear of the seed drill. Safety chains must also be in place to prevent the loss of control in the event of hitch pin loss.
NH3 application rate controllers
Because of the danger of seed damage by NH3, it is advisable to use an NH3 rate controller rather than a fixed orifice meter. A controller is better able to ensure that the correct rate of NH3 is being applied. Without a controller, there is a danger of overapplication of NH3, particularly if the meter is not adjusted to compensate as the day warms up. Overapplication is especially dangerous when the seed bed is dry and when NH3 is applied through a double shoot opener.
Several models of NH3 controllers are available: Dickey John, Raven, Micro-Trak, Field Electronics. The Dickey John, Raven and two models of Micro-Trak have been evaluated and the results are reported in Testing of NH3 Controllers (Alberta Farm Machinery Research Centre/Prairie Agricultural Machinery Institute Evaluation Report 723).
To accurately measure the flow of NH3, most controllers use a heat exchanger to cool the NH3 below -34°C so that it remains as a liquid. Similar to a cold flow converter, there is not much pressure left after the heat exchanger, flow meter and control valve. Therefore, the distribution lines to the shank must be arranged to ensure uniform flow under gravity. There should be no sags in the lines, particularly after the final distributor. If there are low points in a line, the cold liquid accumulates there until the line fills, and then the pressure builds enough to force the full line to empty. This results in overapplication for some distance along the seed row, causing poor or no crop emergence for several feet of that row.
Controllers need to be calibrated for ground speed and for flow through the meter. All monitors come with instructions for calibration and for setting up the control unit for the desired application. Properly calibrated controllers keep the application rate within 2 to 3 kg/acre (5 pounds/acre) for application rates of 20 to 75 kg/acre (40 to 160 pounds/acre). Controllers account for changes in daily temperature and changes in travel speed.
Application rate controllers can change the application rate on the go if the need for more or less nitrogen in certain areas of the field is known. Recent controller designs have a computer communication port so that a computer, with the necessary program information and real-time global positioning, can set the NH3 meter to a preplanned nitrogen rate for each area of the field.
Additional hardware
The addition of NH3 to a direct planter results in many more hoses, fittings, manifolds and so on. These have to be carefully arranged, so the wings of the planter lift without causing kinking or pinching of the lines.
Cooling by NH3 causes frost to form on the lines. The frost collects dirt that falls from the lines as mud. The mud usually falls on the operator who is performing other maintenance. Therefore, items such as pressure gauges and rate controllers should be positioned to allow easy access for maintenance and adjustment.
Ground openers
The ground opener is the part of the planter most affected by the use of NH3. Two concerns must be addressed: soil freezing on the openers and NH3 escaping from the band.
Soil freezing on the opener: The cooling effect of NH3 can cause moist soil to freeze on the opener. The accumulation of soil causes a wider furrow and reduces the flow of soil back over the seed row. This problem is aggravated by cold soil, high NH3 application rates and wet soil.
Some possible solutions to this problem are as follows:
- Modify the opener to isolate the NH3 line from the metal parts of the opener.
- Do not use metal tubing for the NH3. Use the same plastic as that used for the distribution lines.
- Ensure the outlet point of the NH3 tube is below the metal parts of the ground opener.
- Try 1/4-inch diameter NH3 lines (rather than 3/8-inch lines) to reduce the cooling effect of the NH3.
NH3 escaping from the band: If NH3 escapes from the band, it could damage the germinating seed or be lost to the atmosphere. The seed row and the NH3 zone should be at least 25 mm (1 inch) apart. Use an NH3 detection kit to check the performance of the ground opener.
Several factors can result in NH3 escaping from the band. The soil may be lumpy, leaving open spaces between the NH3 band and the seed row or the soil surface. Not enough soil may be flowing back over the NH3 band because the soil is too wet, the equipment is moving too fast, the soil is freezing on the opener, or distribution problems are causing temporarily higher rates of NH3.
Some possible solutions to this problem are as follows:
- Try the solutions given above for soil freezing on the opener if soil freezing appears to be causing the problem.
- Use seed-row-covering harrows or packer wheels behind the opener to ensure soil is replaced on the seed row.
- Try increasing the packing pressure.
- Try changing the travel speed (try going slower, in most cases), changing the opener depth or modifying the opener to increase the flow of soil back over the band.
- Check for NH3 distribution problems such as sags in the lines in cold flow systems. Cold liquid accumulates in the sags until it is forced out suddenly at a high rate.
- Find a drier field to plant if this one is too wet and nothing else works.
Soil compaction in wheel tracks
NH3 supply wagons are generally pulled behind the planter, so the wagon tires run on the soil above the planted seed. If the pressure on the ground is too great, the soil will be too dense for the seedling to push through. Crop emergence damage will be most noticeable in wet soils and clayey soils.
The first solution to this problem is to reduce the tire air pressure to the minimum required to carry the fully loaded wagon. In most cases, this level is considerably below the pressure recommended on the sidewall of the tire. See Solving the Wheel Track Dilemma in Direct Seeding (Agdex 519-12) for more information. Some attempts have been made to change the wheel tread width, so the wagon tires do not run in the same line as the tractor or air seeder tank.
Other application issues
- Check that seeds are staying in the seed band, and not falling into the fertilizer band.
- Maintain and adjust NH3 equipment properly. Poor equipment or improper adjustment may reduce the effectiveness of applications.
- NH3 may be corrosive to metallic parts containing copper, zinc or silver (anything described as brass or bronze).
- A cellular telephone is very useful for coordinating NH3 refill schedules. Delays in delivery of NH3 could prove costly to the planting operation.
NH3 Safety Issues
NH3 is a hazardous substance. Personal contact with NH3 is dangerous at any concentration.
Safety protection and first aid
- Always wear safety apparel including eye protection when working on or around NH3 equipment. The eyes are the part of the body most sensitive to NH3 damage. Eyes have few blood vessels for cooling and very little water, and they do not grow new tissue readily.
- You can smell NH3 at a concentration of 50 parts per million (ppm). It has sharp, pungent odour. It is safe up to 100 ppm for several hours. At 400 ppm, the eyes are irritated and exposure should be avoided.
- Contact with liquid NH3 is the most common accident. The liquid causes a caustic burn from its chemical makeup and a freeze burn as it absorbs water from the skin (the word "anhydrous" means it seeks water).
- Flooding the exposed parts with water is the most immediate need and, in fact, the only first aid needed until full medical attention is received.
- If liquid is spilled, do not remove clothing until flooded with water. The frozen cloth may tear away the flesh.
Safe operation of NH3 systems
- Ensure the NH3 system is correctly designed, assembled and regularly maintained.
- Always use a pressure tank tested to 250 psig to hold NH3, not an LPG tank!
- Turn the equipment and stay upwind if a leak occurs.
- Any coupling between air drills, air tanks and the nurse tank needs to be protected by safety chains, locking draw pins and safety break-away fittings.
- Do not bend hoses, tighten fittings or separate connectors when under pressure.
- Drain all hoses and lines, including the line at the ground opener, before working on any part of the NH3 system. Make sure they are empty. If a plugged NH3 line is removed from the opener, it can spit out liquid NH3.
- Know the correct sequence to open and close valves to purge the system of NH3. Rate controllers have special purge controls.
- Remember that NH3 vapour is combustible if it is 16 to 25 per cent by volume in air and has an ignition source.
- Take a course - and include your helpers - on safe handling of NH3.
Source: Agdex 519-20. May 1998. |
|